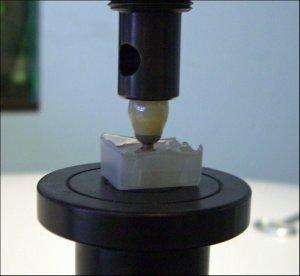
Shrinking Time-to-Market of Dental Implants Medical device researchers are inherently motivated to accelerate their research and development stages given the urgency to bring new dental implant designs to market as quickly as possible. One approach to shrink time is to perform step-stress accelerated life testing rather than to test each sample to failure at varying stress levels. The intent is to reduce the time it takes to produce a traditional SN curve. The traditional testing process of creating an SN curve takes more time and consumes more test samples. Each data point on the SN curve consumes a test coupon in the process of producing a specific stress – life data point. To produce a curve of five data points would require testing five coupons, each at different load levels. In contrast, the step-stress accelerated life testing technique (Hellsing 1980; Manda et al. 2009; Reliasoft 2011) requires fewer test samples and less time. In research performed using a TestResources test machine located at New York University, Dr. Paulo G. Coehlo tested the effect of microthread presence and restoration design (screw versus cemented) in dental implant reliability and failure modes. In his research, Dr. Coehlo broke down 18 specimens into three groups using the step-stress life-testing method of accelerated testing. According to his research, “Based on the mean load to failure from a single load to failure test, three step-stress accelerated life-testing profiles were determined for 18 specimens of each group which were assigned to mild (n = 9), moderate (n = 6), and aggressive (n = 3) fatigue profiles (ratio 3 : 2 : 1, respectively). These profiles were named based on the step-wise load increase that the specimen will be fatigued throughout the cycles until a certain level of load, meaning that specimens assigned to a mild profile will be cycled longer to reach the same load level of a specimen assigned to the aggressive profile (Abernethy 2006). The prescribed fatigue method was step stress accelerated life-testing (SSALT) under water at 9 Hz with a servo-all-electric system (TestResources 800L; TestResources Inc. Corporate Headquarters, Shakopee, MN, USA). Fatigue testing was performed until failure (bending or fracture of the fixation screw, and/or bending, partial fracture or total fracture of the abutment) or survival (no failure occurred at the end of step-stress profiles, where maximum loads were up to 600 N). (Nelson 2004; Coelho et al. 2009; Silva et al. 2009)” To learn more about the work of Dr Paulo G Coehlo PhD, Assistant Professor of Biomaterials and Biomimetics, Director for Research, Department of Periodontology and Implant Dentistry New York University, take a look at his scientific lecture entitled “Bicon Dental Implant Design Overview.”
Recommended Test Machine
Static and fatigue forces up to 50 kN (11,250 lbf)
Frequency ratings up to 75 Hz
Oil-free, all electric actuator for clean test conditions
Lower purchase, operating, and maintenance costs than hydraulic equivalents