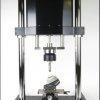
Introducing a new dental implant design to market is a daunting task with an impressive reward. Dental implants are rising in popularity as the Baby Boomer generation turns to research advances in the dental field. Although the market begs for innovation, researchers must consider many challenges in the face of market approval. Constrained by deadlines and budgets, you must prove your design and develop your product. The regulatory aspects are challenging and consume time and resources. Typically mechanical static and fatigue tests are not only required of your device but of predicate devices as well. Mechanical tests may be helpful during the research and development phase and are needed to meet regulatory submission requirements of your 510K. The FDA does not require a 510K planning meeting or even dialogue. That said, we recommend you contact the FDA early in your process to understand their view of expectations. It is a wise choice to pursue a meeting of minds to maximize the chance of succeeding through the FDA on the first try. Contact us as soon as topic of testing arises – we offer experienced application engineering support at no charge. Testing for all types of implants TestResources can assist with testing a variety of dental implants according to the FDA’s guidelines. Currently, the most popular variety is the root-form endosseous dental implant device. They are characterized by four geometrically distinct types: basket, screw, solid cylinder, and hollow cylinder. The root-form endosseous dental implant device refers to the fixture that is surgically implanted into the patient’s bone. That device is surgically placed in the bone of the upper or lower jaw arches to provide support for prosthetic devices, such as an artificial tooth, in order to restore the patient’s chewing function. The endosseous dental implant abutment device is used with the root-form endosseous dental implant to aid in prosthetic rehabilitation. The implant has boomed in popularity due to the secure and stable nature through osseointegration with the bone. After the root-form endosseous dental implant is surgically placed and has healed, the endosseous dental implant abutment device is permanently attached to it in a second surgical procedure. The endosseous dental implant abutment extends above the gum, i.e., it is the transgingival component, which serves as the support for the artificial tooth or other prosthetic. However, if the endosseous dental implant includes an integral transgingival component, it does not need to be used with an abutment. Fatigue testing solutions The FDA recommends that you conduct fatigue testing for devices that: consist of angled abutments; are implant or abutment designs that are significantly different from predicate devices; or have design features or technological characteristics that have not been previously cleared for market. Although there is no mention in the FDA Guidelines regarding testing per ISO 14801, a review of that test method is encouraged. The FDA recommends that you test the finished device or components that have undergone the same manufacturing processes as a finished device. You should explain how the properties of your device show adequate device performance. Some implants do not use a separate abutment component. However, for those that do, the FDA recommends that you test the assembled implant/abutment system. The FDA advises to set up testing to ensure that the implant or implant/abutment system is subjected to both compressive and shear (lateral) forces, with no lateral constraint occurring. Testing conditions should mimic actual intraoral use as much as possible. The FDA also recommends that you perform testing of angled abutments at the greatest angulation intended (i.e., the worst case scenario). Abutment angulation greater than 30 degrees should be supported by clinical data. The test setup should clamp the implant so that the implant’s long axis makes a 30 degrees angle with the loading direction of the testing machine, unless you are testing an angled abutment of greater than 20 degrees. For angled abutments, the test setup should leave at least 10 degrees of the angulation uncorrected (i.e., a 30 degrees abutment should be tested with the implants long axis at 40 degrees and a 25 degrees abutment should be tested with the implants long axis at 35 degrees). The implant should be supported 3mm below the anticipated crestal bone level, simulating 3mm of bone resorption. For endosseous dental implants that include materials in which corrosion fatigue has been reported or is expected to occur, or for systems that include polymeric components, the FDA recommends that you perform fatigue testing in water, in normal saline or in a physiological medium at 37C, at 2 Hz test frequency. You should determine the maximum load (endurance limit) your device can withstand for 2,000,000 cycles. For all other systems, it may be appropriate to perform the test in air at 20 degrees C, at test speeds of 3 to15hz frequency for 5,000,000 cycles. The FDA suggests that you begin testing at a load of approximately 80% of the static failure load of your device system and decrease the load until the endurance limit is reached. The FDA recommends that you test two (preferably three) specimens to failure at each load, and three specimens at the endurance limit. If any of the specimens fail at the expected endurance limit, The FDA recommends that you reduce the load and repeat the tests until a load is reached at which preferably three specimens reach the required number of cycles (2,000,000 or 5,000,000, depending on the test medium). The FDA recommends that you test 4 or more loads and 12 or more specimens. The FDA also suggests that you identify the critical failure point and the location of failure initiation on the device component that fails. Failure is defined as material yielding, deformation, or fracture. The FDA recommends that you compare testing results observed for the claimed predicate device(s). You should include a graph of the load versus number of cycles curve along with testing results and data presented in tabular form. You may use an alternate approach to the load versus number of cycles curve. This may allow the use of fewer samples. One approach is to select a load that is 10% below the static failure load of the device system. The FDA recommends testing 5 or more samples at the selected load. All samples should withstand 5 million cycles. If any samples fail, The FDA recommends that you test 5 additional samples at a slightly lower load. If you use this alternate approach, The FDA recommends that you perform the testing in a simulated physiological solution as described above unless the materials are not subject to corrosion fatigue and there are no plastic components. Tensile, Shear and Bend Static Test Requirements for Metallic Coatings The FDA indicates that you should also test the static tensile and shear bonding strengths between the coating and the implant surface. They recommend the following standards, where appropriate to your device’s composition: ASTM F1160-98 Shear and Bending Fatigue Testing of Calcium Phosphate and Metallic Medical Coatings ASTM F1147-99 Tension Testing of Calcium Phosphate and Metal Coatings ASTM F1501-95 Tension Testing of Calcium Phosphate Coatings ASTM F1658-95 Shear Testing of Calcium Phosphate (replaced with ASTM F1044) ASTM F1659-95 Bending and Shear Testing of Calcium Phosphate Coatings on Solid Metallic Substrates (replaced with ASTM F1160) The FDA also recommends that you include static tensile and shear bonding strengths of the coating to the implant. They recommend the following standards, where appropriate to your device’s composition: ASTM F1044-95 Shear Testing of Porous Metal Coatings ASTM F1147-99 Tension Testing of Calcium Phosphate and Metal Coatings ASTM F1160-98 Shear and Bending Fatigue Testing of Calcium Phosphate and Metallic Medical Coatings ASTM F1580-95 Titanium and Titanium-6% Aluminum-4% Vanadium Alloy Powders for Coating Surgical Navigating standards TestResources can help you navigate the standard hurtles. Our application engineers are available for free consultation about the complexities of testing. Call an engineer today. The above information is intended to increase awareness of mechanical testing guidelines set by the FDA. In no way does performance to these recommendations or testing standards guarantee market placement
Applicable Testing Standards
- ISO 14801 Fatigue Dental Implants Test Equipment
- ASTM F1044 Shear Testing for Calcium Phosphate and Metallic Coatings
- ASTM F1147 Tension Testing for Calcium Phosphate and Metallic Coatings
- ASTM F1160 Shear Bending Fatigue Testing for Calcium Phosphate and Metallic Coatings
Recommended Test Machine
Static and fatigue forces up to 50 kN (11,250 lbf)
Frequency ratings up to 75 Hz
Oil-free, all electric actuator for clean test conditions
Lower purchase, operating, and maintenance costs than hydraulic equivalents
Recommended Testing Accessories
Designed in accordance to ISO 14801
Fatigue rated
Fixed 30° incline
Cup and probe dimensions made to customer specifications
Designed in accordance to ISO 14801
Fatigue rated
Adjustable incline
Can be adjusted in both x- and y-directions