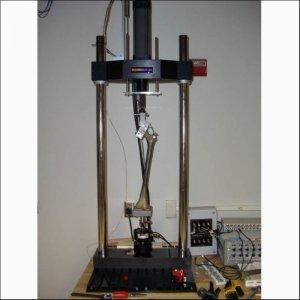
Like all joints in the human body, the hip experiences complicated loading profiles. The hip is also characterized by complex joint kinematics due to its structure as a ball-in-socket joint. For example, during the first 10% of the gait cycle after heel contact the joint undergoes simultaneous flexion, adduction, and internal rotation. Mechanical testing of the hip joint provide better understand of how these motions affect contact stresses between the femoral head and acetabular cup and stresses within the supporting ligaments and tendons of the hip. Unlike most bones in the human body, the femur experiences significant internal moments during normal use. Due to the angle between the femoral neck and shaft, loads applied to the femur at the hip generate a significant bending moment. Mechanical testing of the hip joint and femur give researchers a greater understanding of the femur's internal stresses resulting from the many loading profiles experienced at the hip. This information is crucial for understanding fracture behavior and developing prosthetic hip implants. The large loading within the hip joint also affects wear of the articular cartilage. Over decades of use, cartilage on the hip’s articulating surfaces may no longer provide the cushioning necessary to comfortably carry out daily activities and participate in physical activity. The material properties of cartilage obtained from tension, compression, and indentation force deflection tests, along with the wear patterns observed in fatigue experiments, can be used in the construction of computational models of the hip and development of joint repair and replacement treatments. Images courtesy of the Southern California Orthopedic Institute and The Encyclopedia of Science. The modular design and expandability of TestResources' biomedical testing systems are well suited to customize a solution for the complex loading and fixturing requirements of hip joint testing. Contact a TestResources application engineer to help design the best biomechanical test solution for your current and future research.
Recommended Test Machine
Static and fatigue forces up to 50 kN (11,250 lbf)
Frequency ratings up to 75 Hz
Oil-free, all electric actuator for clean test conditions
Lower purchase, operating, and maintenance costs than hydraulic equivalents
Force ratings up to 50 kN (11,250 lbf) and torque ratings up to 180 Nm (1,600 lbf∙in)
Can apply axial and torsional loads simultaneously
Performs both static and dynamic tests
All electric and oil-free operation
Recommended Testing Accessories
Allows for testing in temperature-controlled water or saline solution
PID controlled temperature up to 45°C (113°F)
Size is optimized per application
Accompanied by a broad set of accessories that are designed for biomedical baths