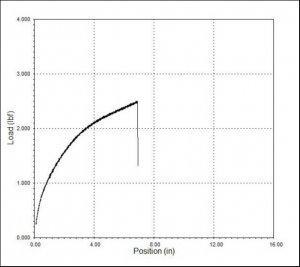
ASTM D429 test standard determines the adhesion of rubber to rigid metal substrates. This test standard is divided into methods A through H. Common application examples that use tests in ASTM D429 are vehicle engine mounts, vehicle suspension bushings, rubber-coated metal parts, and rubber-lined tanks and containers. Most of the tests involve orthogonal tensile strength or peel strength of the adhesion interface. Some of the tests are aimed at shear strength of that adhesion interface. Our engineers are familiar with ASTM D429 and can help guide you through the testing process with the proper equipment. Although our engineers can provide guidance, we recommend you purchase the official ASTM D429 International Standard to achieve the best results.
Test Procedures for ASTM D429
Method A
Test Method A helps determine the static adhesion strength of rubber to metal. Method A of ASTM D429 is used to determine adhesion values in instances where users feel this design is more reflective of an actual product and where control tests have been set up as a result. The sample also lends itself to testing the effectiveness of different processing techniques and various adhesive systems.
Samples for Method A are cylinder assemblies consisting of a cylinder of rubber 3.2 mm thick by 39.9 mm in diameter (1250 square mm area) volcanized between two round pieces of metal with smooth finished surfaces interfacing with the rubber on both ends like a sandwich. The metal pieces are made with tabs on the backsides for gripping in the test machine.
Mount the vulcanized standard test specimen in the tensile testing machine using care in centering and adjustment so that the tension shall be uniformly distributed. Apply a steady tension load until the rubber either separates from the metal surface or ruptures. Record the total force at the time of failure. ASTM D429 Method A requires a constant rate or constant speed of 0.40 to 0.04 mm/s (1 to 0.1 in./min). The grips for holding the specimen in the testing machine depend on the type of specimen. ASTM D429 Method A requires universal or swivel ball seats to permit proper centering of the load during the test.
Method B
Method B of ASTM D429 is intended to determine the adhesive strength of rubber to metal bonding agents by 90 degree peel strip test. The results are obtained by measuring the force necessary to separate a rubber from a metal surface. The data obtained indicate the strength of adhesion along a line across the width of the rubber strip being separated from a metal plate at a 90 degree angle.
The specimen for this method should be a strip of rubber 6.3 mm thick by 25 mm wide by 1125 mm long. The strip is volcanized to a piece of metal which is 1.6mm thick by 25mm wide by 60mm long. The bonded area is 25mm by 25mm in the middle of the metal piece.
To begin testing, place the test specimen in the jaws attached to the fixed grip with the separating edge toward the operator. Before the load is applied, strip the rubber from the metal plate by using a sharp knife. Place the tab in the grip and apply a steady load at a test speed of 50 mm (2.0 in.)/min until separation is complete. ASTM D429 Method B requires a constant rate or constant speed of 0.83 - 0.08 mm/s (2 - 0.2 in./min). At the end of the test you will need to record the force vs displacement. Peel force is indicated in pounds per square inch of length of the peel line.
Method C
Test Method C of ASTM D429 helps determine the adhesive strength of rubber-to-metal bonding agents when applied to conical or cone-shaped samples. This test combines tensile and shear forces in the rubber specimen material. It may apply to vibratory or vibration applications, although this test is not dynamic.
Figure 7 of the official ASTM D429 standard refers to Method C, but can be confusing to readers. In the Figure 7 diagram, the specimen is shown in a horizontal position, when in reality, the specimen would be placed vertically in the test machine. The upper and lower parts of the specimen are metal cones with slots or threads for connecting to the tensile test machine. The middle of the specimen is rubber which bonds the two cones together. The test machine should be equipped with swivel joints above and below to ensure uniformly distributed tensile force tensile force through the specimen assembly. For this method, run the tensile test machine at 2 inches/minute. Data from this test will be a typical tensile force plot (force vs displacement).
Method D
Test Method D helps determine the adhesive strength of rubber-to-metal bonding agents when the bond is formed after the rubber has been vulcanized. Vulcanizing is consists of a chemical reaction with sulfur and heating which improves the mechanical properties of rubber. Rubber is typically bonded to metal during the vulcanizing or heating process, but this method is for glue or other materials that are used after the rubber is made via vulcanizing.
To prepare the specimens for Method D, 6 rubber pucks are mounted in an assembly with a clamp to hold compressive force. Each puck should be .5 inches thick by 1.14 inches diameter. The assembly is cured in a 150 degree Celcius oven for one hour. Next, take the assembly out of the oven and take it apart to create six test specimens. Each specimen will consist of a rubber puck with 2 pieces of metal.
Once the samples have cooled, clamp the bonded assembly to the tension testing machine using tensile grips. Run the tensile tester at a constant rate of 2 inches/minute until the bonded assembly breaks. Loads as high at 10,000 pounds can be common. The test is an orthogonal tensile test where the puck is pulled apart in tension. Either the rubber material fails internally or at the adhesion surface to the metal. Once the test is complete, you will want to record the force vs displacement.
Method E
Method E of ASTM D429 determines the adhesive strength of rubber tank lining to a tank wall using a 90 degree strip test. Results are obtained by measuring the pull load necessary to separate a rubber strip from a metal surface at a 90 degree angle. This test is almost identical to Method B, except it applies exclusively to the rubber lining of a tank wall. Prepare the rubber specimen for this test by vulcanizing it to the metal material of the tank. Make sure that a 1 inch by 1 inch tab is kept from bonding by covering it with tape. This section will be used to clamp in the jaws of the grip.
Next, place the specimen in the jaws attached to the fixed grip with the separating edge toward the operator. Place the tab in the grip and apply a steady load at the rate of 50 mm (2.0 in.)/min until separation is complete.
Method F
Method F is used to measure the adhesive strength of rubber to metal bonding agents. The adhesion values are obtained by measuring the force in an axial direction that is necessary to separate the bonded rubber from the metal component. The metal to rubber interfaces are convex. This geometry promotes interfacial failures.
Create specimens that are 25 mm thick with a 29 mm diameter. Next, mount the test specimens in the threaded grips of the tensile test machine. Apply the tension load at 2 inches per minute until the rubber either separates from the adhesive surface or until the rubber ruptures. Record the total load at the time of failure.
Method G
Method G of ASTM D429 measures the bond strength of rubber to metal components with a double shear cylindrical specimen. This test is often used to find which adhesive is best for the given rubber. The specimens are placed into the shear test fixture and the shear stress is placed on the bond line. A shear test is done until a break occurs at a depth of 5 mm at the rubber-metal bond interface.
Method H
Method H is used for determining relative bond durability between adhesives with a quadruple shear test. First, pull a quality control test piece from each molded batch to determine that 100 per cent adhesion is obtained prior to environmental exposure or laboratory storage with a pre-strain.
Next, the test pieces should be pre-strained by pulling in a test machine to just above the desired pre-strain and inserting a nylon block between the central metal plates to maintain the prescribed prestrain. Then subject the test pieces to the chosen environmental conditions.
Place your specimens in the tensile test machines and pull to failure each test piece which remains sufficiently intact, including those exposed to the chosen environmental conditions and the control test pieces, and record the peak force required to do this.
Advice From Our Engineers
The ASTM D429 standard describes methods to perform these tests with deadweights as an alternative to using a test machine. We highly recommend not using deadweights as those are outdated methods of retrieving data. It is difficult to measure the data correctly and provide consistent results.
ASTM D429 Recommended Test Equipment
Our engineers recommend using a 220Q Universal Test Machine to perform the various Methods A through H. Although these tests range from tension to peel and require a variety of forces, on of our engineers could configure a 200 Series test machine to perform the variety of tests that you require. This test machine is suggested because it has a long travel, which is preferred because rubber coating tests to enlongate quite a bit when stretched.
The Q controller and XyLive Software are the best choice to pair with the 220Q Universal Test Machine. XyLive is the best choice to enable the test engineer to visually monitor the progress of the test vs the data on the computer screen. The test engineer can learn more about the uniformity of the rubber coating from this visual monitoring.
Peel Grips and Accessories
Pneumatic vice grips such as G240kP are recommended to grip the rubber peel strip because the rubber elongates and necks down. Pneumatic grips are active in that they maintain the same gripping force even as the specimen necks down. This will help avoid slipping in the test. Manual vice grips may also work but must be tightened very tight. You will also need a 90 degree sliding peel table for the 90 degree test methods in ASTM D429. We also recommend serrated jaws on your grips to avoid sample slipping. Slippage in grips will be a big challenge in testing rubber coating of metal because coating adhesion must be strong but rubber material necks down, also called Poisson effect. As force is applied in one direction the material shrinks in the orthogonal direction.
Give one of our engineers a call today and they can help guide you through the ASTM D429 test process with the best machine configuration for your requirements.
Recommended Test Machine
Forces up to 10 kN (2,250 lbf)
Low force tabletop systems
Modular series of five frame options with adjustable test space
Affordable testing option for tension, compression, bend, peel and much more
Forces up to 5 kN (1,125 lbf)
Low force tabletop systems
Tests at speeds up to 2,500 mm/min (100 in/min)
Best for high travel or high elongation test requirements
Force range of 5 kN to 600 kN (1,125 lbf to 135,000 lbf)
Adjustable test space
The most popular choice for static tension and compression tests
These dual column testers are available in both tabletop and floor standing models
Recommended Testing Accessories
Load ratings from 1 kN to 10 kN (225 lbf to 2,250 lbf)
Maximum specimen thicknesses of 7 mm or 8 mm (0.28 in. or 0.31 in.)
Works very well with flat, thin specimens
Eccentric design increases gripping force with tension
Rated to 10 kN (2,250 lbf)
For testing adhesives or films at a 90° angle
Rolling table maintains the peel angle throughout the test
Standard length of 300 mm (11.8 in) - other lengths available
Rated to 0.6 kN (135 lbf)
Maximum specimen thicknesses from 8 mm to 50 mm (0.3 in. to 2.0 in.)
Clamp force up to 1.2 kN (270 lbf)
Quick and simple specimen setup for a wide variety of applications