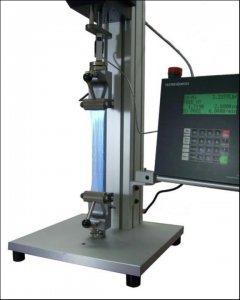
As a delicate challenge, thin plastic sheeting can be difficult to test without bending and slipping. Plastic sheeting is commonly tensile tested using methods found in ASTM D882. ASTM D882 pulls the plastic until it breaks in order to measure elongation, tensile modulus, tensile yield strength, and tensile strength at break.
ASTM D882
ASTM D882 is very similar to ASTM D638, but D882 is designed specifically for thin sheeting and film less than 1 mm (0.04 in.). Another difference is that in D882 samples can be cut into simple rectangular strips rather than the typical dumbbell shape. Tensile properties of the plastic can be measured with grip separation, extension indicators, or displacement of gage marks.
The tensile modulus of elasticity is an indicator of the stiffness of thin plastic sheeting. Make sure to maintain precise control over all test conditions to increase the chance of test result reproducibility. The tensile energy to break (TEB) is the total energy absorbed per unit volume of the specimen up to the breaking point. Sometimes the TEB is referred to as toughness. It is used to evaluate materials that are subjected to heavy abuse or that can stall web transport equipment in the event of a machine malfunction in end-use applications. However, the rate of strain, specimen parameters, and especially flaws can cause large variations in the results. In that sense, we advise caution in utilizing TEB test results for end-use design applications.
Testing Procedure
For ASTM D882, a few trial runs may be necessary to select a proper combination of load range and specimen width. To begin, place the test specimen in the grips of a testing machine, taking care to align the long axis of the specimen with an imaginary line joining the points of attachment of the grips to the machine. Tighten the grips evenly and firmly to the degree necessary to minimize slipping of the specimen during testing.
Next, start the machine and record the load versus extension. When total length measurements between grips are used as the test area, record load versus grip separation. When an extensometer is used, record load versus extension of the test area measured by the extensometer. If modulus values are being determined, select a load range and chart rate to produce a load-extension curve of between 30 and 60 degrees to the X axis. For maximum accuracy, use the most sensitive load scale for which this condition can be met. If tensile energy to break measurements is being determined, provision must be made for integration of the stress-strain curve.
A universal testing machine can be used for ASTM D882. There are also many options for special line contact jaws that are used to establish gage length. By means of our plastic testing expertise and modular product design, we will help find the testing solution that is right for you. Give one of our application engineers a call today for help with creating the best budget and testing plan according to ASTM D882.
Recommended Test Machine
Forces up to 10 kN (2,250 lbf)
Low force tabletop systems
Modular series of five frame options with adjustable test space
Affordable testing option for tension, compression, bend, peel and much more
Forces up to 5 kN (1,125 lbf)
Low force tabletop systems
Tests at speeds up to 2,500 mm/min (100 in/min)
Best for high travel or high elongation test requirements
Force range of 5 kN to 600 kN (1,125 lbf to 135,000 lbf)
Adjustable test space
The most popular choice for static tension and compression tests
These dual column testers are available in both tabletop and floor standing models
Recommended Testing Accessories
Rated to 220 N (50 lbf)
Designed in accordance to ASTM D882
Maximum specimen thickness of 8 mm (0.31 in)
Rated to 500 N (112 lbf)
Maximum specimen thickness of 6 mm (0.23 in)
Pneumatic design allows for quick specimen setup
Consistent clamping force between tests
Gage lengths of 25 mm and 50 mm (1.0 in. and 2.0 in.)
Maximum elongations from 130 mm to 500 mm (5.0 in. to 20 in.)
Comes with adjustable and magnetic mounting base
Rated from 1°C to 125°C (34°F to 257°F)
Designed for applications that deal with very elastic material, such as rubber
No inherent gage length, allowing it to be used for almost any sized specimen
Maximum travel ratings up to 1,100 mm (43 in)
Adjustable clips allow for gripping onto various specimen thicknesses and materials
Standard temperature range of -155°C to 620°C (-247°F to 1150°F)
Accompanied by a broad set of accessories that are capable of withstanding the heat or cold
PID controlled internal temperature
Mounts directly to the test frame
Cuts test specimens from stock material
Available for a wide variety of ISO and ASTM standards
Consistent specimens for consistent results
Manufactured with tool steel to resist damage and wear over time