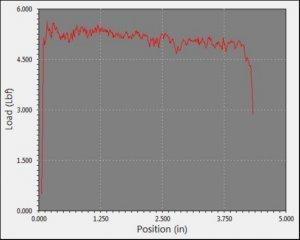
PSTC-101 is a standard test method to measure peel adhesion strength in pressure sensitive tapes. PSTC-101 is a Harmonized International Standard. These types of standard tests are created under the understanding that societies and other technical bodies from a variety of countries have agreed to consolidate their similar standards under the auspices of ISO. This standard addresses the various types of peel tests appropriate for pressure sensitive tape.
Pressure sensitive tape designers need to perform several different peel tests in order to ensure a good quality design of their tape, as well as ensure manufacturing consistency. PSTC-101 is similar to the tests required in ASTM D3330, another popular peel test standard, but with some minor differences. Our engineers can help guide you through the PSTC-101 testing process, but we recommend you purchase the official PSTC-101 Harmonized International Standard to achieve the best results.
Preparing the Specimens
PSTC-101 requires your sample sizes to be 24 mm wide by 300 mm long. In order to create uniform specimens, you should use a TestResources pre-sized sample cutter. After you create the samples, make sure to clean the rigid surface or testing plate with a high quality solvent. Next, apply the tape sample to the clean surface using a TestResources weighted sample roller to ensure consistent and repeatable pressure.
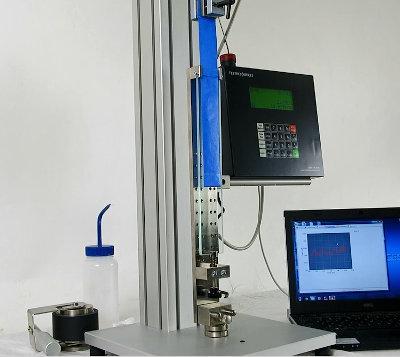
PSTC-101 Test Procedure
PSTC-101 is very similar to the test methods involved in ASTM D3330. As in ASTM D3330, PSTC-101 defines Methods A through F to measure adherence with 180 degree and 90 degree peel tests. The following tests should be performed:
- Method A is a 180 degree peel test of test tape to a standard steel panel
- Method B is a 180 degree peel test of tape to its own backing
- Method C is a 180 degree peel test of double-sided stick tape to a standard steel panel
- Method D is a 180 degree peel test of single or double-sided stick tape to its liner
- Method E is a 180 degree peel test of transfer tape adhesion to a standard steel panel
- Method F is a 90 degree peel test of tape to a standard steel plate or other surface of interest
Test Procedure for Methods A through E
- Use a TestResources weighted sample roller to adhere a tape sample onto the 180 degree peel fixture
- Screw the 180 degree peel fixture into the lower end of the Peel Tester
- Pull the tape up into a “U” shape and clamp the free end of the specimen in the upper vice grip.
- Run the peel test machine at the speed required per individual method
- Record the average force and displacement values of five tests per method
Test Procedure for Method F
- Use a TestResources weighted sample roller to adhere a sample onto a steel testing plate
- Side and secure the steel plate into the lower sliding fixture of the Peel Tester
- Pull up the free end of the tape and clamp it into the upper vice grip so that the tape is now at a 90 degree angle
- Run the peel test machine at the rate given in PSTC-101
- Record the force and displacement values given and average the numbers over 5 tests
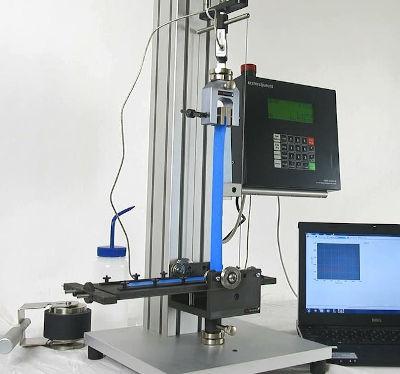
Advice From Our Engineers
In 180 degree peel tests it is easy for the tape to rub on its own backside, causing friction. This friction is an error measured by the sensitive load cell you need to use for peel testing. For the 180 degree peel tests in PSTC-101, our G227 or G240k grips can offset the jaws enough to ensure that the tape does not rub its own backside during the peel pull.
TestResources 90 degree sliding peel tables are designed with a cable pulley assembly which attaches to the peel test machine’s actuator above the load cell. This assembly causes the horizontal table to slide sideways during the peel pull. This keeps the peel interface directly under the load center which ensures the 90 degree peel angle throughout the entire peel.
Do not use a force gauge to try to perform a peel test by pulling manually. Adhesives are visco-elastic materials and their strength varies based on the rate of the pull. Manual pulling will cause high variations in peel force. Read our blog article to learn more about this.
PSTC-101 Recommended Test Equipment
A 100P250 Peel Tester is recommended for PSTC-101. The 100P250 consists of a vertical load frame, an electromechanical actuator, load cell, a tocuhpad test controller, XY test software and peel grips. For PSTC-101, we would configure a small 25 pound load cell for this low force peel test. Our load cells measure loads accurately (+/- 0.5% of reading) from full scale rating to 1% of FS.
The peel plot will be an important aspect of data retrieval and therefore we highly recommend our XyPlot software. If you would rather see the data in real-time and study the peel interface at the same time, we would provide you with our XyLive Software.
Peel Grips and Accessories
PSTC-101 requires vice grips to hold the sample in place. We can provide you with our G227 or G240k Mechanical Vice Grips for simple and effective testing. For faster testing results we offer our G229 Pneumatic Grips. These types of pneumatic grips are also helpful in getting the specimen well-aligned in the grips (to avoid the rubbing issue highlighted above) due to the foot activator giving you both hands free to hold the specimen. It is not easy to hold the specimen exactly perpendicular in the grips while you are cranking a manual vice grip.
Recommended Test Machine
Forces up to 10 kN (2,250 lbf)
Low force tabletop systems
Modular series of five frame options with adjustable test space
Affordable testing option for tension, compression, bend, peel and much more
Forces up to 5 kN (1,125 lbf)
Low force tabletop systems
Tests at speeds up to 2,500 mm/min (100 in/min)
Best for high travel or high elongation test requirements
Recommended Testing Accessories
For testing adhesives or films
Peeling surface is a 152.4 mm (6.0 in) diameter wheel rather than a table
For testing adhesives or films at a 90° angle
Sliding table maintains the peel angle throughout the test
Rated to 10 kN (2,250 lbf)
For testing ahesives or films at a 90° angle
Rolling table maintains the peel angle throughout the test
Standard length of 300 mm (11.8 in) - other lengths available
Rated to 220 N (50 lbf)
Maximum specimen thickness of 8 mm (0.31 in)
Wider model allows for specimens thicknesses up to 46 mm (1.8 in)
Cost effective option for low force testing
Rated to 500 N (112 lbf)
Maximum specimen thickness of 6 mm (0.23 in)
Pneumatic design allows for quick specimen setup
Consistent clamping force between tests
Rated to 1 kN (225 lbf)
Maximum specimen thicknesses from 10 mm to 50 mm (0.39 in. to 2.0 in.)
Simple design can be used for a multitude of tensile applications
Inexpensive and reliable
Rated to 0.6 kN (135 lbf)
Maximum specimen thicknesses from 8 mm to 50 mm (0.3 in. to 2.0 in.)
Clamp force up to 1.2 kN (270 lbf)
Quick and simple specimen setup for a wide variety of applications