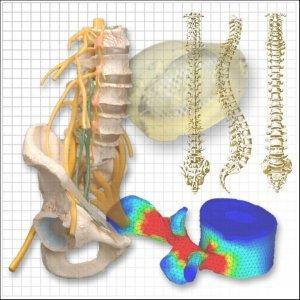
The spine is a complex joint and so research on biomechanics and flexibility remains. Mechanical static and dynamic tests include multi-axial and complex simulation of spinal segments under different conditions. Mechanical tests of spinal devices and implants such as rods, pedicle screws, hooks, plates, cages, constructs, intervertebral fusion devices, nucleus replacements, and intervertebral disc prostheses normally follow ASTM or ISO standards, including axial compression, torsion, flexion-extension, lateral bending, lateral shear, and anterior-posterior shear. Both static and fatigue tests such as these can be performed on electrodynamic axial and axial torsional test machines. Combined biaxial tests are performed on all sorts of spinal functions and devices including fixation, constructs, segments and other components require combined axial and torsional tests. Tests apply static and dynamic forces while acquiring test data. Load bearing activities are simulated on subsections such as functional spine units or lumbar and cervical sections. In the end, spinal implants require extensive mechanical tests due to the consequences of potential catastrophic failure. Simple static testing is also required to evaluate the compressive, tensile and torsional loading required to fracture a spinal device. Fatigue life tests are critical because fatigue failure is more common than catastrophic failure. Loading test samples with load-controlled sinusoidal waveforms is most common, and tests last in excess of ten million cycles.
Applicable Testing Standards
- ISO 12189 Fatigue Spinal Implant Test Equipment
- ASTM F1264 Torsion & Bend Fatigue Test Equipment for Intramedullary Fixation Devices
- ASTM F1717 Spinal Implant Static and Fatigue Test Equipment
- ASTM F1798 Static and Fatigue Properties of Interconnection Mechanisms and Subassemblies Used in Spinal Arthrodesis Implants
- ASTM F2077 Fatigue Compression Torsion Shear Intervertebral Fusion Device Test Equipment
- ASTM F2193 Fatigue Bending Surgical Fixation Spinal Skeletal Test Equipment
- ASTM F2267 Axial Compression Load of Intervertebral Body Fusion Device
- ASTM F2346 Static and Dynamic Characterization of Spinal Artificial Disc Test Equipment
- ASTM F2624 Dynamic Static Spinal Implants Test Equipment
- ASTM F2706 Fatigue Static Spinal Implants Test Equipment
- ASTM F2790 Static Dynamic Tests Lumbar Prostheses Test Equipment
Recommended Test Machine
Static and fatigue forces up to 50 kN (11,250 lbf) Frequency ratings up to 75 Hz Oil-free, all electric actuator for clean test conditions Lower purchase, operating, and maintenance costs than hydraulic equivalents
Force ratings up to 50 kN (11,250 lbf) and torque ratings up to 180 Nm (1,600 lbf∙in) Can apply axial and torsional loads simultaneously Performs both static and dynamic tests All electric and oil-free operation