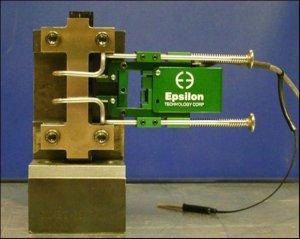
Continued advancements in the design and manufacture of engineered composites has allowed composite materials to work their way into the products we use everyday. By definition, a composite material is simply any material that contains two or more constituent materials. The materials that make up a composite are chosen either to enhance or supplement the material properties of the individual materials. The typical material combination seen in today's composites is a material that performs well in tension (fiber or rebar) paired with a material that performs well in compression (epoxy, ceramic, or cement). The most common modern advanced composites are fiber-matrix composites and they can be manufactured with polymer, carbon, metal, or ceramic matrix and an extremely wide range of reinforcement fiber including, carbon, graphite, boron, aramid, and glass.
The compressive strength of modern advanced composites is primarily determined by the compressive strength of the matrix material. Composites compression tests are commonly conducted using specially designed grips and fixtures. These grips aid in the proper alignment of test samples, help ensure failure in the specific mode being tested, and prevent improper load application which could damage the composite microstructure and adversely impact test results. For some compression tests of composites, it is important to ensure that the specimen is not able to rotate and failure does not occur by buckling. These rotational and buckling constraints help to constrain loading and failure to the desired material plane. Test fixtures are also designed to be used in a wide variety of test environments, which are necessary to recreate the real life application conditions of composite materials. The creation of these environments is achieved through the use of saline baths for testing composites used in marine, biological, and outdoor environments and high temperature environmental chambers for composites used in the aviation, aerospace, and automotive industries.
ASTM and ISO have developed standard test methods for testing composite materials in compression. The standards provide methods that can be recreated, ensuring materials are tested in the same manner and conditions and allowing test results validation between manufactures and customers. Popular test methods for compression testing of composite materials are ASTM D3410 for polymer matrix composites with unsupported gage section by shear loading, ASTM D4762 for polymer matrix composite materials, ASTM D5449 for hoop wound polymer matrix composite cylinders, ASTM D5467 for unidirectional polymer matrix composites using a sandwich beam, ASTM D6484 for open hole compressive strength, ASTM D6641 for polymer matrix composites using combined loading compression, ASTM D6742 for filled-hole compressive strength of polymer matrix composite laminates, ASTM D695 for rigid plastics, ASTM D7137 for compressive residual strength of damaged polymer matrix composites, ISO 20504 for ceramic composites at room temperature, and ISO 3597-3 for glass roving reinforced plastics. Fiber reinforced composites are often have lower strength in compression than tension; however materials such as reinforced ceramics can exhibit extremely high compressive strengths. Depending on the individual sample size and composition of the composite, the compressive force requirements can be met with either tabletop or floor standing machines. The machine families below can be matched to the wide range of composite materials being tested. Since grips for composites tend to be custom, many of the grips below are designed for specific ASTM or ISO test methods, and others are representative of grip families which can be customized for composites compression testing. Contact a TestResources application engineer to determine the best machine and grip combination for your exact composite testing needs.