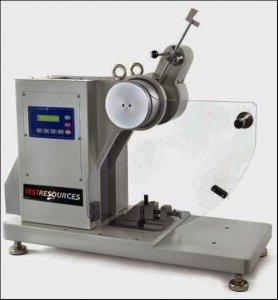
The Charpy impact strength test, or Charpy v-notch test, is a high strain rate test used to determine the amount of energy a material can absorb when impacted by a large impulse. The Charpy impact test was first used by the French engineer George Charpy in 1905. Charpy impact strength testing is a simple test in which a notched or unnotched specimen is struck by a pendulum arm to determine the impact strength of that specimen. The impact energy absorbed in impacting a plastic specimen in a Charpy test is assumed to be equal to the difference between the potential energy of the pendulum and the energy remaining in the pendulum after impacting the plastic specimen. Corrections accounting for friction and air-resistance losses must also be made to determine the true impact resistance of the plastic. Impact strength is an important design parameter to consider in plastic structures because it quantifies how a plastic material will withstand sudden shocks or large impulses.
Charpy impact tests are used to determine the toughness of a material, the ductile-brittle transition temperature (DBTT) and ductility of a plastic material. Plastics will absorb impulses impacts differently then static load impacts, often high strength plastics are also quite brittle, or having low impact strength. By testing plastics with the Charpy test method the impact resistance of the plastic can be determined. Charpy impact testing can also be used to determine the sensitivity of notched plastics specimens. Impact resistance of plastic notched specimens measures how will a cracked plastic specimen will withstand an impact. Measuring notch sensitivity of plastics with the Charpy test can be applied to plastic designs. Charpy testing results of notched specimens are measured in energy loss per unit cross-sectional area, for example J/m2 or ft-lb/in2. Toughness of a plastic describes how much energy the plastic material will absorb while plastic deformation is occurring, and can be determined with Charpy impact resistance testing. ISO 179 and ASTM D6110 serve as standard test methods for Charpy impact resistance testing of plastics. These standard Charpy test methods are used for quantifying the impact resistance of plastic materials cover testing of notched plastic specimens. Results of standardized Charpy impact strength tests should be used for comparison between materials for quality assurance purposes. ISO13802 is the international standard for the verification of pendulum impact testing machines. TestResources 402 Series Charpy impact strength test machine meets the requirements set by ISO 13802. The 402 Series test machine is also designed to meet the Charpy impact strength testing requirements of ASTM D6110. Email or call our staff with questions regarding Charpy impact resistance testing equipment.
Applicable Testing Standards
- ISO 13802 Pendulum Impact Test of Plastics | Machines
- ASTM D6110 Charpy Impact Resistance of Notched Specimens of Plastics
Recommended Test Machine
Energy capacities from 1 to 50 J (Izod) and 0.5 to 150 J (Charpy)
Convenient tabletop design
150° impact angle
Automatically calculates impact energy from the test
Force range of 5 kN to 600 kN (1,125 lbf to 135,000 lbf)
Adjustable test space
The most popular choice for static tension and compression tests
These dual column testers are available in both tabletop and floor standing models
Recommended Testing Accessories
Forms rubber or plastic test specimens from stock material or from individual particles
Variable temperature and pressure to form samples to different specifications
Capable of cooling the newly formed specimen at a user-specified time
Force outputs of 9,100 kgf, 27,000 kgf, or 45,000 kgf (10 ton, 30 ton, or 50 ton)
Stamps test specimens from soft rubber, leather, or similar stock materials
Consistant samples for consistant results
Force outputs of 900 kgf or 3,000 kgf (1 ton or 3 ton)
No need to press by hand
Forms plastic test specimens from plastic particles
Variable temperature and pressure to form samples to different specifications
Capable of cooling the newly formed specimen at a user-specified time
Outputs 9,100 kgf (10 ton) of force