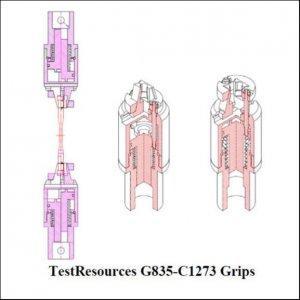
Advanced engineering ceramics have a number of material properties that have made them one of the most important classes of engineering materials. Ceramics have an extremely high elastic modulus, maintain consistent performance at elevated temperatures, and have great resistance to wear and corrosion, which has contributed to their widespread use as bearing surfaces, heat resistance, and insulation applications. The ability for ceramics to perform at high temperature has made them the go to material for high end automobile brake rotors and pads, space re-entry vehicle heat shields, and ball bearings in high speed and high temperature applications. The use of fiber reinforcement with a ceramic matrix provides an increase in tensile strength and fracture resistance, making ceramics a viable material for structural applications. The strength properties of ceramics can be greatly reduced by the presence of internal and surface imperfections.
Specimen breaks near the grip-sample interface are telltale signs of surface damage or internal crack initiation due to poor or improper fixturing. Proper clamping of ceramic test specimens for tensile tests is achieved by close tolerances for specimen and grip dimensions and parallelism of jaw and specimen clamping faces, for flat test specimens. High quality grips, properly prepared test specimens, and good test procedures will ensure uniform loading of the ceramic samples. Since the high modulus characteristic of ceramics is often a key property for ceramics applications, elongation measurements are important. Due to the low strains present in ceramic materials, strain and elongation measurements must be made using an extensometer or strain gage. Care must be taken to prevent contact extensometers from damaging the ceramic specimen surface. To help prevent extensometer slippage, some test procedures allow the machining of grooves for the placement of extensometer contacts. ASTM and ISO have developed standard test methods to aid in the proper testing of the wide variety ceramic materials. These tests address the various applications of ceramic materials and environments in which they will be used. Popular standards for tensile testing of monolithic ceramic materials are ASTM C1273 for ambient temperature, ASTM C1291 for tensile creep at elevated temperature, ASTM C1361 for tension-tension fatigue, ASTM C1366 for elevated temperature, ISO 15490 for room temperature, and ISO 22215 for tensile creep at high temperature.
Applicable Testing Standards
- ISO 15490 Fine Ceramics Tensile Strength
- ISO 22215 Tensile Creep Ceramics Test Equipment
- ASTM C1273 Tensile Ceramic Test Equipment
- ASTM C1291 Tensile High Temperature Ceramics Test Machine
- ASTM C1361 Tension Tension Fatigue Ceramics Test Machine
- ASTM C1366 Tensile Ceramics Elevated Temperatures Test Machine
Recommended Test Machine
Force range of 5 kN to 600 kN (1,125 lbf to 135,000 lbf)
Adjustable test space
The most popular choice for static tension and compression tests
These dual column testers are available in both tabletop and floor standing models
Recommended Testing Accessories
Satisfies the requirements of ASTM C1273
Designed to grip cylindrical test specimens
Wedge design self-tightens to avoid specimen slippage
Maximum operating temperature options of 500°C or 1200°C (930°F or 2,200°F)
Minimum operating temperature of 300°C (570°F)
PID controlled temperature
Utilizes 120 V or 240 V power
Standard temperature range of -155°C to 620°C (-247°F to 1150°F)
Accompanied by a broad set of accessories that are capable of withstanding the heat or cold
PID controlled internal temperature
Mounts directly to the test frame