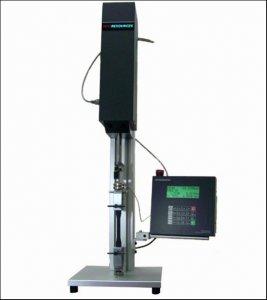
Plastics can be broken into two categories: thermoplastics, and thermosetting polymers. The defining characteristic of thermoplastics is that they do not experience a change in their chemical composition when heated. When thermoplastic polymers are heated above the glass transition temperature the material becomes soft and rubber-like. At cooler temperatures the thermoplastic material is more rigid. This allows thermoplastics to be heated and molded many times. Alternatively, thermosetting polymers get their rigidity from an irreversible chemical reaction. The chemicals that are used to create thermoset plastics cannot be heated and separated. Some common thermosetting polymers include polyethylene, polypropylene, polystyrene, polyvinyl chloride, and polytetrafluoroethylene (PTFE).
The most common uses for thermosetting polymers are epoxy and molds like those used in semiconductors and integrated circuits. Tensile tests of thermoplastics and thermosetting polymers are done to determine mechanical material properties. Plastic tensile tests are done to determine the tensile strength, elongation, failure characteristics, modulus of elasticity, secant modulus, and Poisson’s ratio. ASTM and ISO have a number of tensile testing standards that are related to thermoplastic and thermosetting polymers. The two most common testing standards for plastic tensile testing are ASTM D638 and ISO 527. ASTM D638 and ISO 527 both use a dumbbell (aka dog-bone) specimen that is pulled to failure with a tensile testing machine. These standards are very similar in their testing procedures; however there are a few technical differences that differentiate the two standards. The most significant difference between ASTM D638 and ISO 527 is the method for determining the Tensile Modulus of Elasticity of the plastic specimen, and ISO 527 requires pre-stress of the plastic and ASTM D638 does not. Other ASTM and ISO plastic testing standards are listed below. TestResources has plastic tensile testing machines that can be configured for a wide range of thermoplastic and thermosetting material testing applications. Data output for plastic tensile test include stress strain charts, and analysis for tensile yield, tensile breaking strength, tensile percent elongation at yield, tensile break elongation, nominal strain at break, and modulus of elasticity. Thermoplastic and Thermosetting Plastic Tensile Test Machines & Equipment TestResources has a variety of modular plastic tensile testing machines. These plastic tensile testers are designed and assembled for each testing application.
Applicable Testing Standards
- ISO 527 - Tensile Test of Plastics Composites
- ISO 22088-6 Tensile Environmental Stress cracking plastic Test Equipment
- ASTM D638 Tension Testing for Plastics
- ASTM D882 Tensile Testing for Thin Plastic Sheeting
- ASTM D1623 Tensile Adhesion of Rigid Cellular Plastic
- ASTM D1708 Tensile Testing for Plastics and Microtensile Specimens
- ASTM D2105 Fiberglass Tensile Test Equipment
- ASTM D2343 Tensile Glass Fiber Strands Yarns Rovings Testing Equipment
- ASTM D3826 Tensile Test Degradation End Point in Degradable Polyethylene and Polypropylene
- ASTM D3916 Tensile Testing Pultruded Glass-Fiber-Reinforced Plastic Rod
- ASTM D5083 Tensile Test of Reinforced Thermosetting Plastics Using Straight-Sided Specimens
Recommended Test Machine
Forces up to 10 kN (2,250 lbf)
Low force tabletop systems
Modular series of five frame options with adjustable test space
Affordable testing option for tension, compression, bend, peel and much more
Force range of 5 kN to 600 kN (1,125 lbf to 135,000 lbf)
Adjustable test space
The most popular choice for static tension and compression tests
These dual column testers are available in both tabletop and floor standing models
Recommended Testing Accessories
Rated to 220 N (50 lbf)
Designed in accordance to ASTM D882
Maximum specimen thickness of 8 mm (0.31 in)
Satisfies the requirements of ASTM D638
Load ratings of 20 kN and 50 kN (4,500 lbf and 11,250 lbf)
Maximum specimen thickness of 16 mm (0.63 in)
Self-tightening design resists slippage of the specimen
Satisfies the requirements of ASTM D2105
Designed to test pipes and tubing in tension
Dimensions made to order per specimen dimensions
Self-tightening design resists specimen slippage
Load ratings from 10 kN to 100 kN (2,250 lbf to 22,500 lbf)
Maximum specimen thicknesses from 16 mm to 22 mm (0.63 in. to 0.87 in.)
Pneumatic actuation eases specimen setup
Self-tightening design
Rated to 5 kN (1,125 lbf)
Works well with flat or round specimens
Maximum specimen thickness / diameter of 10 mm (0.4 in)
Standard temperature range of -155°C to 620°C (-247°F to 1150°F)
Accompanied by a broad set of accessories that are capable of withstanding the heat or cold
PID controlled internal temperature
Mounts directly to the test frame
Stamps test specimens from soft rubber, leather, or similar stock materials
Consistant samples for consistant results
Force outputs of 900 kgf or 3,000 kgf (1 ton or 3 ton)
No need to press by hand
Stamps test specimens from soft rubber, leather, or similar stock materials
Consistant samples for consistant results
Force outputs of 900 kgf or 3,000 kgf (1 ton or 3 ton)
No need to press by hand
Forms plastic test specimens from plastic particles
Variable temperature and pressure to form samples to different specifications
Capable of cooling the newly formed specimen at a user-specified time
Outputs 9,100 kgf (10 ton) of force
Forms rubber or plastic test specimens from stock material or from individual particles
Variable temperature and pressure to form samples to different specifications
Capable of cooling the newly formed specimen at a user-specified time
Force outputs of 9,100 kgf, 27,000 kgf, or 45,000 kgf (10 ton, 30 ton, or 50 ton)