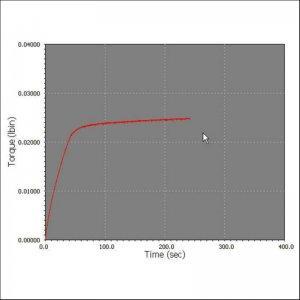
Metal wire is very useful for carrying signals and power, because of its ability to conform to numerous shapes. A good wire material must be able to withstand repeated bending, twisting, and pulling, while maintaining structural integrity and the desired material properties. Wire torsion tests are a measure of wire ductility, and help to ensure sufficient wire strength to withstand normal loads. Typical wire torsion test systems contain one stationary and one moveable grip, with the ability to apply a constant axial load. The axial load ensures that the wire does not bend from the axis of load application or fold over on itself. A popular method of applying the axial load is through a deadweight pulley system, like the one on the test machine pictured. The deadweight ensures a constant axial load throughout the test, regardless of wire shortening or elongation due to material deformation. ASTM and ISO have developed standardized test methods for testing the torsional properties of metal wire. These tests apply an increasing torque until failure, by twisting the wire specimen at a constant angular velocity. Popular methods for torsion testing of wire are ASTM A938 and ISO 7800. TestResources offers a wide range of electromechanical, electrodynamic, and servo-hydraulic torsion and axial-torsion test machines for testing the torsional properties of wire. The torque capacity of these machines ranges from 62 to 17,750 in-lb. The machine featured above is a 160 series torsion machine with a deadweight system for applying a constant axial load on the wire specimen to keep the wire from overlaying on itself or moving out of axis.
Applicable Testing Standards
Recommended Test Machine
Axial Load Capacity: 0.8 to 300 kN (180 to 67000 lbf)
Torsion Capacity: 1 to 300 Nm (9 to 2655 in-lb)
Static and dynamic options available
Torsion Capacity: 1 Nm to 5650 Nm (9 to 50,000 in-lb)
Type: Electromechanical Gear or Electrodynamic Direct Drive
Available in both horizontal and vertical orientations